Step #1 in Basement Remodeling – RadonSeal Concrete Sealer
Whether you’re hiring a contractor or are tackling a basement renovation on your own, when it comes to finishing a basement and basement remodeling the first rule of thumb is: do not start the project until you know the basement is dry! Basement water issues can cause serious damage and ruin your investment.
Protect Your Basement Remodeling Investment With A Concrete Sealer
Before finishing the basement, deep-seal your concrete against water seepage, water vapor, and soil gases like radon. RadonSeal™ penetrates deep into new or old concrete (up to 4 inches), reacts and seals it internally to provide:
- WATERPROOFING – Prevents water seepage
- DAMP-PROOFING – Reduces humidity
- RADON MITIGATION – Reduces soil gas
- CONCRETE PRESERVATION – Denser, stronger concrete
The spray-on application is quick and easy for basement remodeling contractors or homeowners. RadonSeal™ Penetrating Concrete Sealer is non-toxic, non-flammable, and emits no VOCs and best of all, THE SEAL IS PERMANENT!
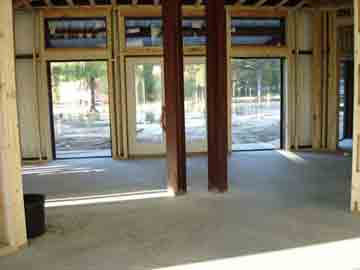
How Basements Slowly Self-Destruct
Moisture problems are the most common complaint of homeowners and most basements develop water seepage within 10 to 15 years. Additionally, one out of five homes in the US have elevated radon levels. Why?
1. Concrete Is Naturally Porous (12%-18% air) – when concrete cures, surplus water escapes and creates a network of interconnected capillaries, much smaller than a human hair (10-100 nm). The capillaries draw water from the ground by wicking action or let in water under hydrostatic pressure. The pores also let in water vapor and radon gas, which are pulled in by the lower air pressure and concentration indoors.
2. Concrete Is Highly Alkaline (pH 9 -11) – The alkalis disintegrate exterior waterproofing coatings – even the best membranes are guaranteed for only 5-10 years. The plastic sheet under the slab (vapor retardant) gets “eaten” by lime from the concrete. As soil and gravel settle, water and soil gases pool in the void right underneath the slab.
Water migration gradually leaches out concrete and makes it more and more porous. As concrete ages, the seepage of liquid water, water vapor, and radon gas steadily increase.
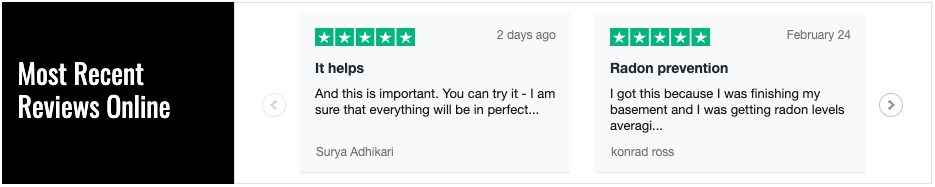
Molds and Mildew Thrive in Finished Basements!
Moisture promotes molds, mildew, dust mites, and other biological air contaminants, which cause allergies, asthma, or other health problems. Ventilation spreads humidity and contaminants through the house.
Molds need high humidity and organic materials to survive. They thrive in carpeting, upholstered furniture, drywall, wood paneling, and moist fiberglass insulation. Mildew munching on cellulose produces volatile organic compounds (e.g. aldehydes), which we detect as musty odors. Moldy furnishings have to be discarded!
Consequently, the key to fighting or preventing molds and mildew is removing the source of moisture. Seal your basement with RadonSeal™ against capillary water seepage and water vapor.
Customers’ feedback and tips on Sealing Damp Basements against Moisture and Molds.
Protect Your Basement Remodeling Investment
Even if your basement looks dry, moisture is pouring in as invisible vapor and by evaporation of water seeping through capillaries. The basement is by far the largest source of moisture in your home (over 15 gallons/day). Covered floors and walls in finished basements trap moisture and eventually cause:
- DAMP or WET BASEMENT – High humidity, water seepage, condensation
- MOLDS and MILDEW – Mold and mildew spread by ventilation through the house
- MUSTY ODORS – From molds devouring organic materials in the basement
Basement finishing is a cost-effective home improvement project. But first, seal all under-the-grade concrete with RadonSeal™ to protect your investment and your family’s health. Afterward, seal or caulk any openings, gaps, or cracks.
According to HomeGuide.com, the average cost of a midrange basement remodeling project was roughly $40,000 in 2022.
How Alkalis Attack a Finished Basement
Water carries dissolved alkalis from the concrete and soil. Water vapor condenses on cool surfaces (“sweating walls” in the summer) or when trapped under a covering and activates the alkalis in concrete.
Alkalis dissolved in water attack fatty acids in paints and adhesives (saponification). All paints or surface sealers will peel or blister. If you install floor tiles, sheet vinyl, linoleum, glue-on wall panels, it will trap moisture and the glue will disintegrate. The alkalis even attack carpeting, floor coverings, and the concrete itself. Lime from inside the concrete forms efflorescence (whitish minerals), which easily lifts paints and floor tiles.
RadonSeal reacts with the lime and alkalis in concrete, stops efflorescence, and seals the capillaries against water and vapor.
You Already Have a Moisture Problem?
Without fixing existing water seepage or dampness problems, a basement should not be finished. Homeowners have various options:
Exterior waterproofing of the foundation walls is a proven and expensive solution (say $12,000) but does little against moisture seeping through the slab. Interior perimeter drains (say $6,000) under the slab do little for seepage through the walls. Interior channels (say $3,000) take water seeping through the walls to a sump pump but do nothing for the slab and release lots of vapor and radon. These methods do little against water vapor seeping in through the concrete.
Waterproofing paints or surface sealers applied on the interior cannot hold back negative-side water pressure or efflorescence for long. Cementitious waterproofing coatings stop active seepage and last longer. But over time, they will crack or separate and they cannot stop the main source of moisture – vapor.
Never cover the floor or walls with a plastic sheet! It cannot stop water being drawn inside by the force of capillary suction or as water vapor – it just traps it. After a couple of years, you would likely discover musty odors, molds, and mildew. Epoxy coatings or urethanes are very strong and durable but not so much on concrete slabs exposed to moisture from the ground. They trap all moisture and after several years, will bubble and crack.
Running dehumidifiers is expensive(say $40/month) and they pull in more moisture through the concrete, speeding up its deterioration.
If the foundation walls and slab are poured concrete, or concrete block, (not lightweight blocks) and still sound, RadonSeal will seal it against the seepage of water and vapor. After application, you can increase ventilation in the area or install a dehumidifier/fan for several days to speed up drying and curing. Afterward, repair any cracks, gaps, or openings (see our basement crack repair guide for details).
How NOT to Finish Basement Walls!
Most finished basements are constructed with interior insulation – stud wall framing filled with paper-faced fiberglass batts, often covered with a polyethylene vapor barrier or fiberglass “blanket” insulation with impermeable vinyl or aluminum foil surfaces (sometimes called “the diaper” for the odor it causes). But according to the latest research, this common construction is unsuitable for the building home industry due to serious problems with mold, decay, and odors. (Building Science Consortium) It traps water vapor coming from the exterior, small leaks let humid interior air reach the cold concrete, and any groundwater seepage cannot dry out.
Basement walls with an interior vapor barrier can never dry if they become wet. “The use of vapor barriers (polyethylene or vinyl wall coverings) has caused many building failures and facilitated the growth of molds in many buildings. The widespread use of double vapor barrier basement wall in Minnesota has resulted in many failures, in some cases within a year of construction.”
Avoid interior finishes impermeable to water vapor such as vinyl floor coverings (only 0.1 to 0.5 perms), OSB sheathing (instead of plywood), oil (alkyd) paints, or vinyl wallpaper.
How to Build Interior Basement Walls
Heat loss from an uninsulated basement can account for up to one-third of the heating cost in an average home. The walls must be insulated on the exterior or interior for the house to be called “energy efficient.” How much insulation? Department of Energy recommends total R-values for existing houses in most regions R-11 for interior basement walls (R-19 for crawlspace walls).
Exterior insulation of extruded polystyrene panels would be best. It stops exterior moisture and keeps the walls warmer, which prevents condensation, and lets them dry out to the interior. But it has not been widely accepted because of damage during backfilling, needed design modifications, and concerns about termites and insects.
Interior insulation must be moisture-tolerant. It also must be permeable to water vapor coming in from the exterior and must allow any groundwater seepage to dry out. We need not a “vapor barrier” but an “air barrier.” Insulation materials meeting these permeability requirements: up to two inches of unfaced extruded polystyrene (R-10), four inches of unfaced expanded polystyrene (R-15), three inches of closed cell medium density spray polyurethane foam (R-18), or ten inches of open-cell low-density spray foam (R-35).
We must also stop moisture-laden interior air from contacting the cold concrete surface, in order to avoid condensation in the summer.
The proper solution for finishing basement walls:
- Seal the concrete with RadonSeal™ against water seepage and water vapor.
- Glue on the walls extruded polystyrene (XPS) sheathing (1-2 inches) or expanded polystyrene (ESP or “beadboard” is cheaper but more permeable to moisture, less moisture-resistant and has a lower R-value). Seal joints either with tape or fiberglass mesh and mastic.
- Hold the panels in place permanently by wood furring strips attached through the XPS by power-driven nails, or build 2″x3″ 24” o.c. wood stud wall attached to the floor and floor joists. If additional cavity insulation is desired, fill in the frame wall with unfaced batt insulation.
- Polystyrene is flammable and must be covered with a 15-minute fire-rated material – 1/2 inch gypsum board without paper facing. Hold up from the floor at least 1/2 inch.
- Use only latex paints (semi-permeable to moisture) on the gypsum board.
A simpler alternative solution – avoid any plastic vapor barriers and build a stud wall about 1-inch away from the concrete wall, using unfaced insulation batts (or slash the paper backing with a knife) and gypsum board. The open space allows for evaporation of water from the concrete and avoids direct contact of moisture-sensitive materials with the concrete. And by all means, seal the concrete first with RadonSeal™ against water seepage and water vapor.
Radon Gas Problems in Basements
Several years after finishing the basement, you might find that the radon level has increased above the EPA’s action limit (4 pCi/L) and must be reduced to make the house marketable. But once the basement has been finished, you have to get a fan-based radon mitigation system ($1,200 on average). The radon fan and piping will not enhance the house value.
You may want to reduce the radon level to a minimum just to protect your family’s health, particularly, if the children spend lots of time in the finished basement.
Before basement remodeling, seal the concrete with RadonSeal™ to reduce radon to a minimum and to keep it that way.
Flood Protection
Choose interior finishes with consideration for the possibility of flooding from leaky appliances, failed plumbing, overflowing sinks, or exterior surface flooding.
If you have a sump pump, install a backup sump pump to protect your finished basement. Our water-powered and battery-powered pumps are placed above the sump water and provide maximum reliability.
An Ounce of Prevention …
Your finished basement has to hold back water, vapor, and radon and needs a little help.
As the first step, seal the walls and slab with RadonSeal™ penetrating concrete sealer to protect your remodeling investment and your family’s health, to preserve the concrete, and to avoid costly basement repairs in the future.